
Metal Panel Brazing Manufacturing Technology Knowledge
Honeycomb Brazing Induction & Torch Brazing Byron Honeycomb Brazing is most commonly used in jet engine and land base turbines, either OEM or overhaul. At Byron Products honeycomb brazing is one of our.
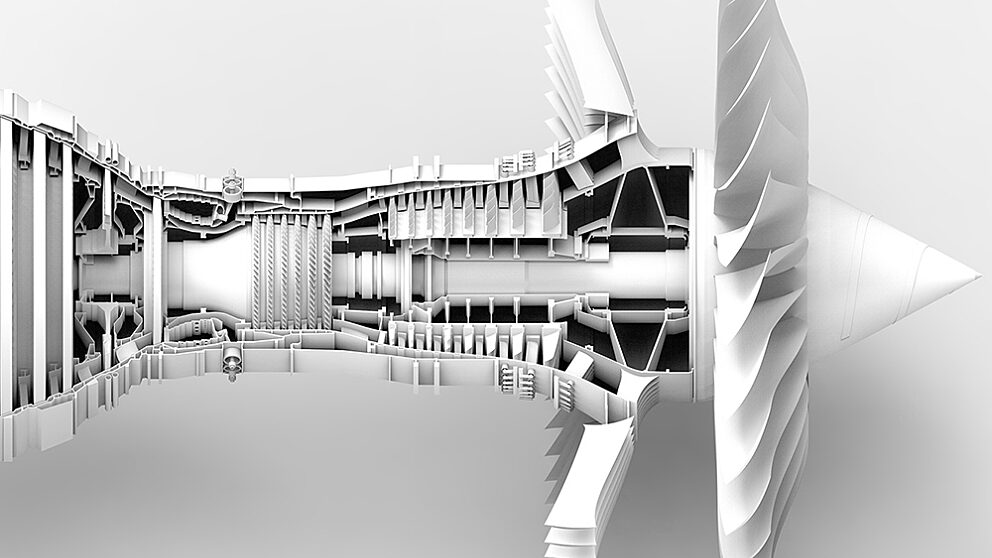
Brazing Vacu Braze
Stainless Steel Request a Quote Our approach to honeycomb brazing has resulted in a high degree of quality and compliance for our aerospace and power generation clients.
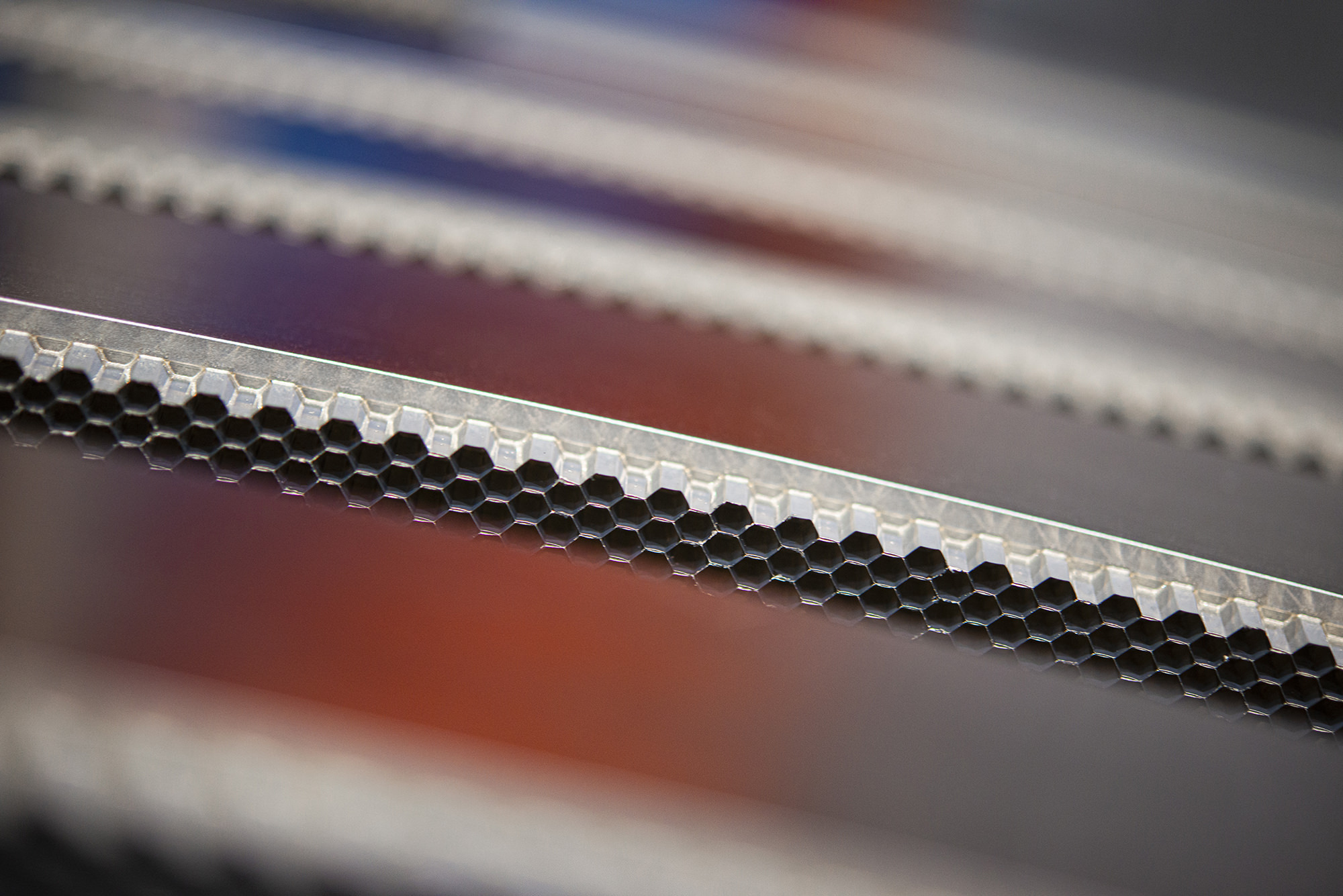
Vacuum Brazing Vacu Braze
August 24, 2022 At Byron Products, we can take care of a wide variety of thermal processing needs - and honeycomb brazing is one of them. For those who don't know, honeycomb brazing is used most commonly in the aerospace industry, and we're proud to say we specialize in this complex thermal procedure.

Hengshi Vacuum Brazing EMI/EMC/RF Shielding Round Shape
For the rub-in behavior of the honeycomb liners, not only the foil material but also the comportment of the composite made up of the foil material, the braze filler material and the interdiffusion zones has to be considered. Keywords brazing, BNi-5, Hastelloy X, honeycomb liner, rub-in, superalloy, turbine 1. Introduction

Brazing Vacu Braze
Abstract. Experts state that certain factors need to be considered to select materials for brazing a honeycomb structure in turbine engines. A popular abradable structure is metallic honeycomb.

Brazing Issue 20210120 Industrial Heating
This work is focused on the checking of the correctness of the brazing process of honeycomb seals to stationary elements of aircraft turbine engines. It describes this process, paying attention to the aspects that have a fundamental impact on whether the seal will be brazed to the base as required, or whether unacceptable areas of non-brazing will appear. The aim of the study was to check the.

Ceramic honey comb block for brazing and soldering. Art and craft
The honeycomb sealing systems are produced by brazing together nickel-based superalloy sheets with a nickel-based brazing metal. This investigation aimed to generate data on the mechanical performance of Haynes 214 metal sheets brazed with the nickel-chromium-silicon filler metal BNi-5 (71 wt.% Ni, 19 wt.% Cr, 10 wt.% Si).

Brazing 20190917 Industrial Heating
For honeycomb seals, braze tape is often preferred. While the customer specifies the width and thickness, the tape can also be supplied with no adhesive or adhesive on one or both sides for convenient placement on the shroud.
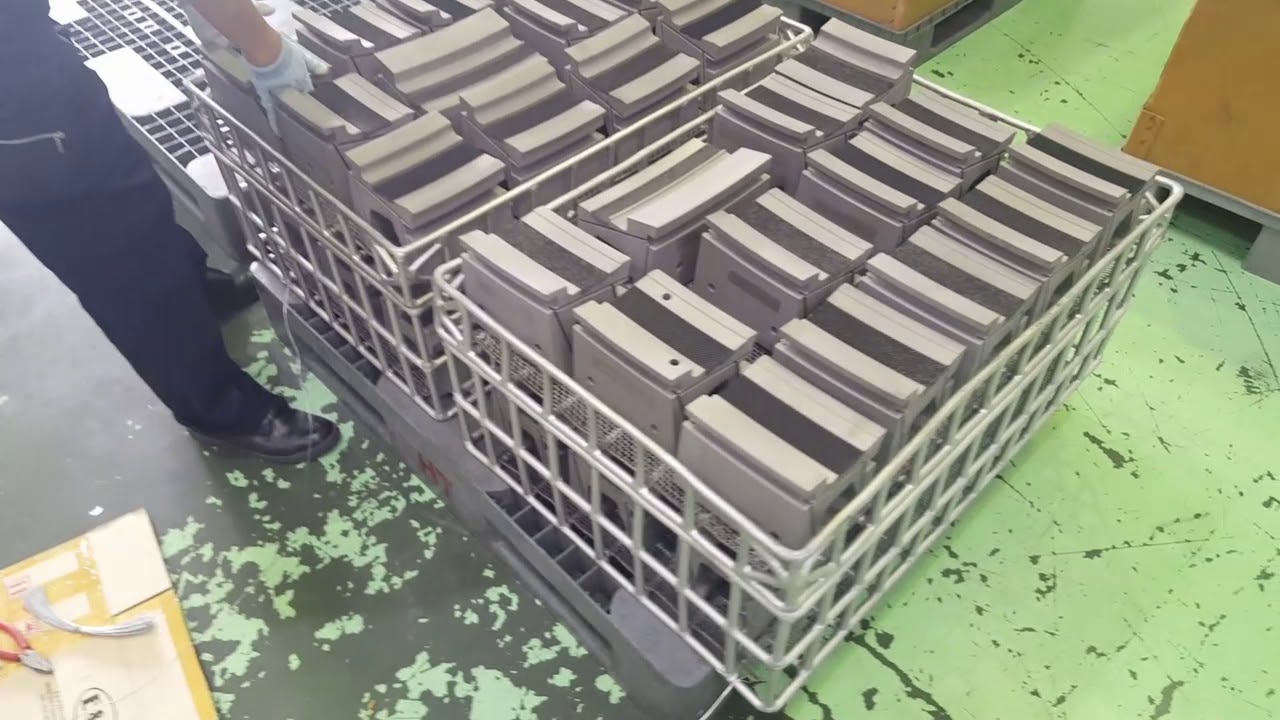
Brazing YouTube
Two primary purposes for using honeycomb for rotor-blade tip seals (rubbing seals, abradable seals, etc.) are: (1) to provide a gas-path seal to prevent hot engine gases from getting around the ends of the turbine rotor blades, and (2) to simultaneously provide a sacrificial surface against which the rapidly rotating blades will rub.
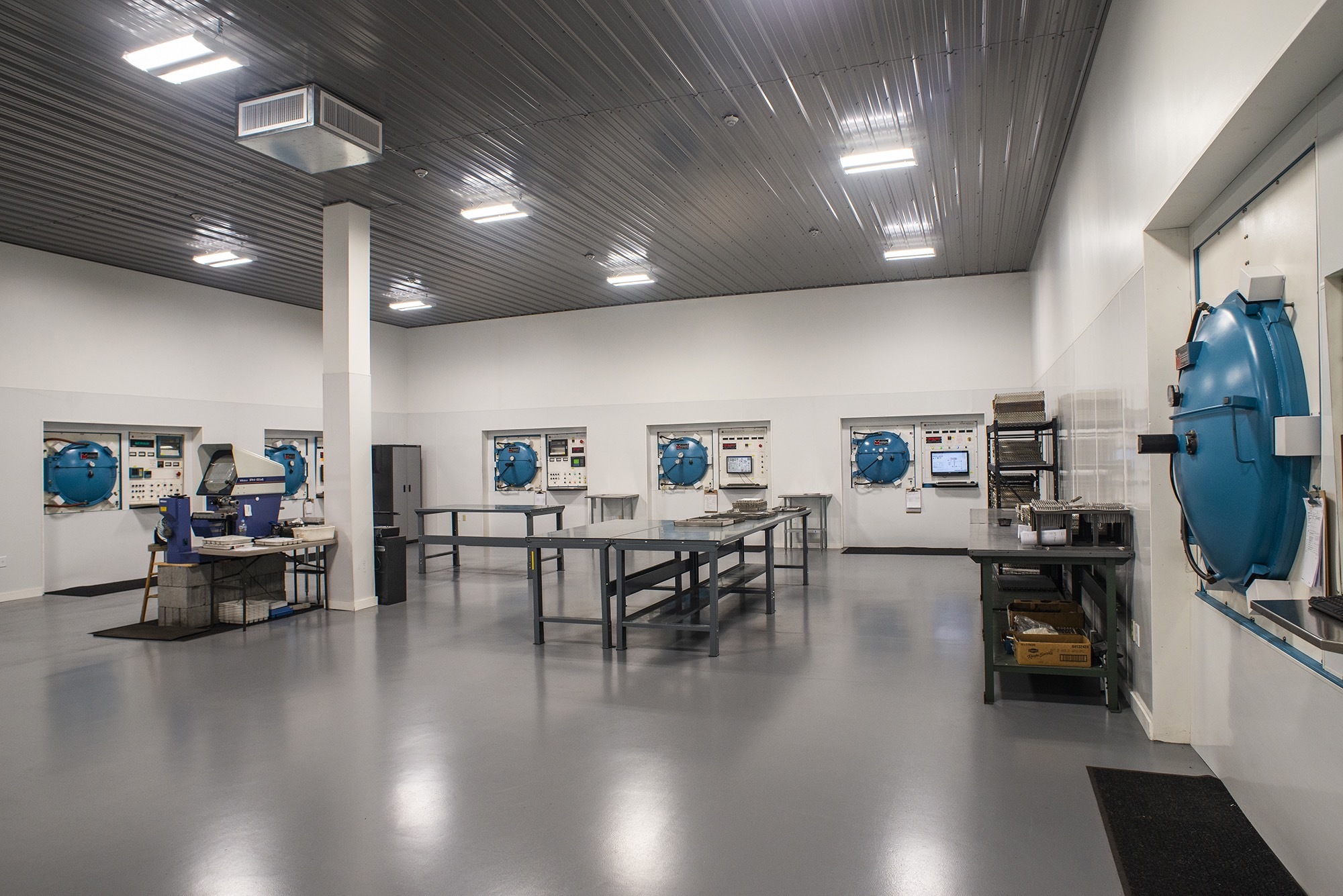
Brazing for Aerospace & Power Generation Vacu Braze
The honeycombs made from nickel-based superalloys are brazed onto backing segments in order to form liners. In this work, the microstructure of Hastelloy X honeycombs after brazing with a nickel-chromium-silicon braze filler alloy is investigated.

Vacuum Brazing Vacu Braze
Thus, the brazing process for honeycomb sandwich structure is very vital to prevent cracking, disjoining, and even destruction of the sandwich structure. For weight-sensitive applications, the metallic sandwich structures with low specific-strength have limited demand. In our design, high Nb containing TiAl (TAN) as face sheet and GH3536 nickel.
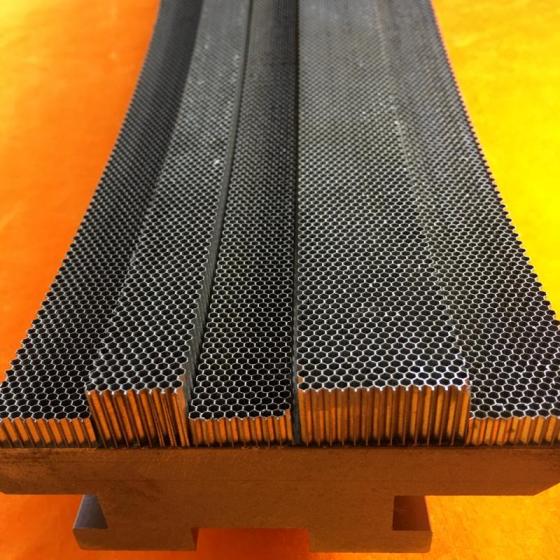
Metal Brazing Seal Design and Manufacturer for Gas/Steam
Honeycomb Brazing. As specialists in honeycomb brazing, we provide solutions widely used in jet engines and land-based turbines. Regardless of your unique requirements or complex designs, our skilled engineering staff is ready to engage in meaningful dialogues, explore your needs, and provide exceptional quality with ultimate customizability.

Brazed carbon fibre/titanium capability Engineer Live
Honeycomb Brazing. Barbara Kuntz. Tags: honeycomb, brazing. Related Articles. Measuring Displacement: Absolute vs Reference. Advanced Laser Marking Processes Solve Manufacturing Challenges. Artificial Intelligence and Machine Learning for Manufacturing: Resistance & Laser Weld Monitoring.
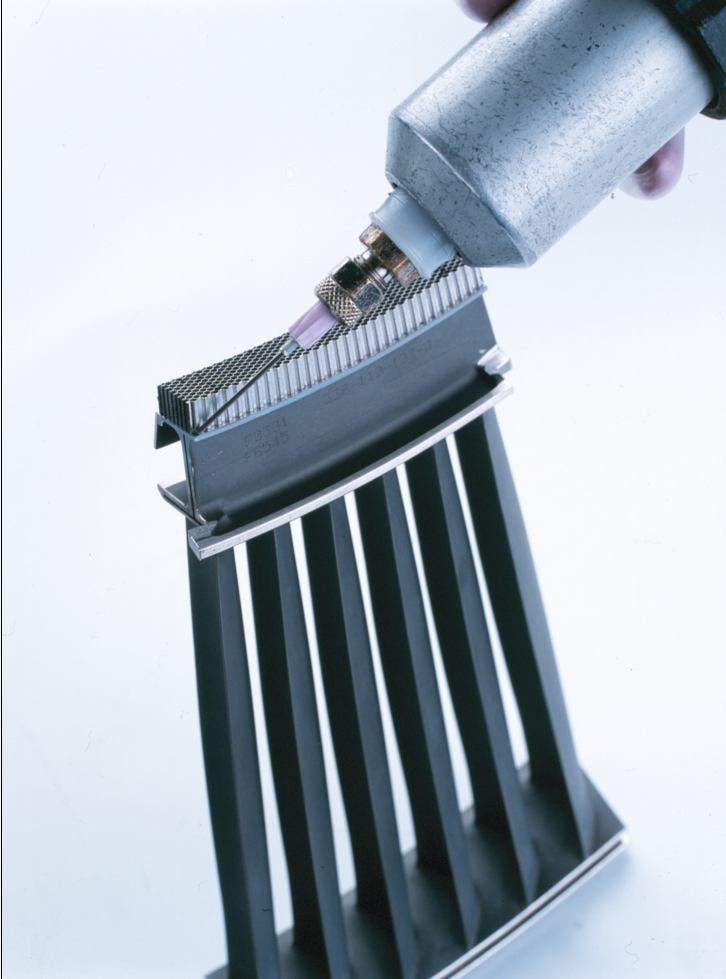
2 Aerospace Technology
A honeycomb structure serves as an excellent gas flow seal and a sacrificial wear-surface to rotating turbine blades in high-temperature turbines. Achieving the ideal honeycomb construction requires careful attention to the amount and placement of brazing filler metal and brazing time and temperature. No Paper Link Available.

Brazing Issue 20210120 Industrial Heating
Selecting Materials for Brazing a Honeycomb in Turbine Engines. To reduce leakage flows in turbo machines, tight operational clearances between stator and rotor parts are desirable. With reduced clearances, the risk of rub contact increases. In such situations, the stator is fitted with an abradable structure or coating that minimizes damage to.
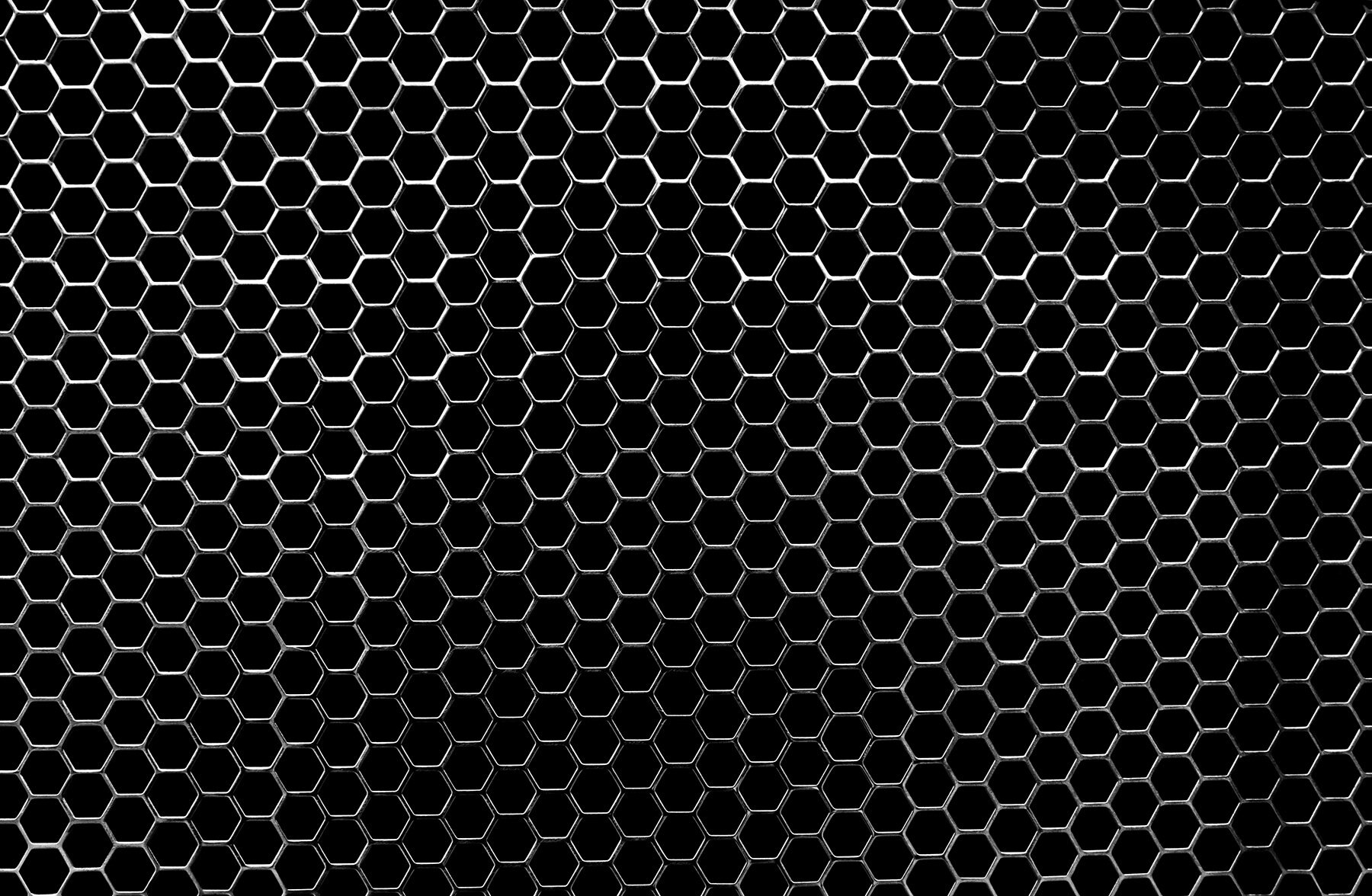
Vacuum Brazing Vacu Braze
A honeycomb structure serves as an excellent gas flow seal and a sacrificial wear-surface to rotating turbine blades in high-temperature turbines. Achieving the ideal honeycomb construction.